The Automatic Meatball Processing Production Line for sale is a high-efficiency, fully integrated solution designed for meat processing plants, food manufacturers, and commercial kitchens aiming to scale up their production with precision and hygiene. This advanced line automates every stage of meatball production—from raw meat preparation to final packaging—ensuring consistent size, texture, and flavor across every batch. Constructed with food-grade stainless steel and compliant with international safety standards (CE, FDA, HACCP), this line is ideal for processing pork, beef, chicken, fish, or plant-based proteins.
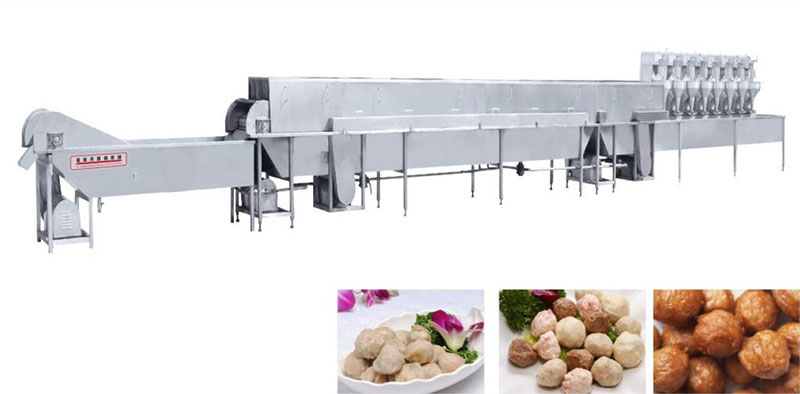
Meatball Production Process
Meat Cutting & Grinding → Mixing & Seasoning → Meatball Forming → Blanching/Cooking → Cooling & Dewatering → Freezing (Optional) → Packaging
Meat Cutting & Grinding Machine: High-capacity grinder with interchangeable plates for coarse or fine grind;
Automatic Mixer/Beater: Dual-shaft mixer with PLC-controlled speed for uniform seasoning incorporation;
Meatball Forming Machine: Rotary forming head producing 50–300 balls/min with adjustable size heads;
Blanching/Cooking Tunnel: Stainless-steel conveyor cooker at 60–80 °C for pre-setting and full-cook options;
Cooling & Dewatering Conveyor: Chilled-air or water spray system removes surface moisture and oil;
IQF Freezing Tunnel (Optional): Air-blast freezer ensures individual freezing at –35 °C to –40 °C;
Automated Weigh-Fill-Seal Packer: Multi-head weigher with nitrogen flush for dry, vacuum or MAP packaging;
Parameter
Equipment | Power Supply | Dimensions (L×W×H) mm | Capacity |
Meat Cutting & Grinding Machine | 7.5–15 kW, 380V, 50Hz | 1200 × 800 × 1400 | Up to 2000 kg/h |
Automatic Mixer/Beater | 5.5–11 kW, 380V, 50Hz | 1600 × 1000 × 1500 | 300–1000 L/batch |
Meatball Forming Machine | 2.2–4 kW, 220/380V | 1000 × 800 × 1500 | 50–300 balls/min |
Blanching/Cooking Tunnel | 15–30 kW, 380V, 50Hz | 5000 × 1000 × 1800 | 300–1000 kg/h |
Cooling & Dewatering Conveyor | 3–5 kW, 380V, 50Hz | 4000 × 1000 × 1600 | Matches upstream capacity |
IQF Freezing Tunnel (Optional) | 30–60 kW, 380V, 50Hz | 6000 × 1500 × 2200 | 500–1500 kg/h |
Automated Weigh-Fill-Seal Packer | 5–8 kW, 220/380V | 2200 × 1500 × 1800 | 20–60 packs/min (varies by pack size) |
Meatball Production Line Features
Full-Line Automation: Integrates cutting, grinding, mixing, forming, cooking, cooling and packing in one continuous line;
SUS304 Construction: All food-contact components are 304 stainless steel, CIP-ready and compliant with global hygiene standards;
Programmable Control System: PLC-driven settings allow recipe memory, portion accuracy and cook-time adjustment;
Optional IQF Freezing Tunnel: Individual quick-freezing preserves shape and extends shelf life for frozen-ball applications;
Meatball Processing Line Advantages
Reduced Labor Costs: Automation cuts manual intervention by over 60%, lowering OPEX;
High Throughput: Scalable modules deliver 100–1 000 kg/h, fitting small to large-scale operations;
Consistent Quality: Precision forming heads and cooking units yield uniform size, texture and internal doneness;
Energy-Efficient Design: Advanced heat recovery and optimized motor drives reduce energy consumption by up to 20%;
Meatball Production Line Benefits
Faster ROI: Higher throughput and lower labor/electricity costs deliver payback within 12–18 months;
Product Diversification: Easily switch between meat, seafood or plant-based recipes by changing mixing parameters and forming molds;
Enhanced Food Safety: CIP piping and sealed cooking tunnels minimize contamination risk, ensuring compliance with CE, FDA and HACCP;
The Automatic Meatball Processing Production Line for Sale delivers a fully automated, energy-efficient and scalable solution—ensuring high throughput, consistent quality and rapid ROI. Ready to transform your meatball production? Leave us an online message now for detailed layouts, machine specs and a personalized quote!